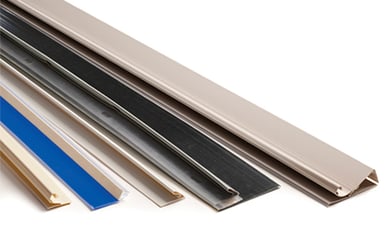
Plastic extrusions may be more cost effective than aluminum or steel components in certain applications.
This is achieved by reducing the number of steps in manufacturing or fabrication processes. The result is better use of labor as well as improvements in lead time.
Plastic extrusion allows for efficient in line operations such as drilling or cutting.
In some cases, multiple plastic materials are coextruded to achieve a mix of performance properties while eliminating the need for offline assembly.
Additional Improvements From Plastic
Replacing metal parts with plastic can deliver several other benefits on top of lower manufacturing costs.
With plastic components, colored polymers are used in place of painting or powder coating, creating significant time savings.
As an added advantage, plastic produces consistent color throughout the entire part. This minimizes the appearance of potential chips or scratches that would be highly visible on a painted surface.
The ability to reduce the overall weight of components is an attractive quality of plastic. In high-moisture applications, such as shower surrounds, plastic can provide mildew resistance. Plastic also may be the solution when anti-static properties are desired.
Work With Us
To determine if a custom plastic extrusion is suitable for your application, Cooper Standard ISG engineers will work with you to consider strength, mechanical, thermal and other requirements.
Part design will be evaluated based on the chosen material to ensure proper performance and manufacturing efficiency.
Contact us today to learn more.
Related Topics: Manufacturing Processes, Engineering and Design, Plastics